Чем и как проводится контроль качества сварных швов на трубопроводах
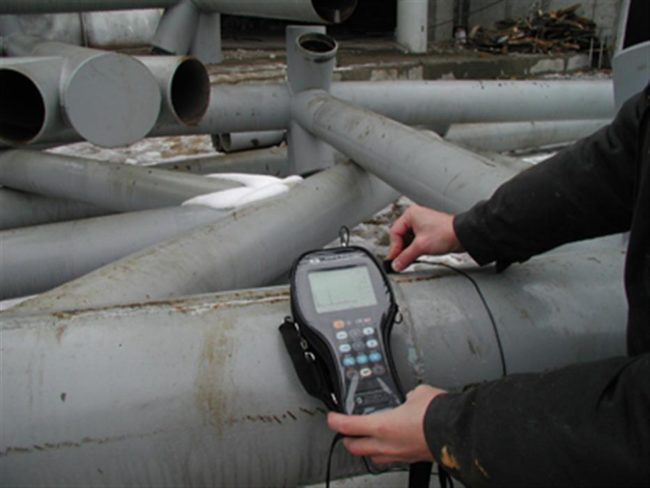
На производстве и в бытовом использовании линии металлических трубопроводов состоят из множества труб, сваренных между собой. Совокупность всех сварных соединений должна обеспечивать герметичность системы. Для этого, все сварные швы подвергают контролю качества. Сваренную конструкцию подвергают контролю без ее разрушения.
Ниже будут рассмотрены основные методы, которые используются для проверки качества сварных соединений, не подвергая их разрушению.
Содержание
Несколько лов о важности такого контроля

Процесс сварки подразумевает нагрев металла и его смешивания во время соединения участков. Нарушение технологии сварки может привести к образованию пустот внутри шва или появлению трещин.
Иногда такие дефекты легко определить при помощи визуального контроля. Трещины или следы не проваренных участков легко заметны на поверхности шва. Если же дефект находится на глубине более 2 мм, прибегают к различным методам дефекации.
К признакам некачественного шва можно отнести множество типов дефектов и необязательно ими должны быть только трещины. Трещина на самом деле является одним из худших случаев в дефектологии швов.
Ниже приведены стандартные названия дефектов на стыках сварных швов трубопроводов.
- Трещины – как уже было сказано, это серьезный вид дефекта. Дефектом, который можно назвать трещиной является участок с длинной гораздо больше ширины. Трещины бывают разные, они необязательно находятся на поверхности шва. Это может быть трещина внутри соединения или же самое худшее – сквозная.
- При выполнении сварочных работ возникают поры газа, которые при охлаждении металла не успевают выйти на поверхность шва. Остывая, они представляют собой пору или же раковину от пузырька газа. Такие дефекты случаются внутри шва.
- Предыдущий дефект в виде пузырька газа может успеть выйти на поверхность и разрушиться снаружи. Этот поверхностный дефект имеет форму кратера. Еще одной причиной образования на поверхности кратеров является обрыв дуги во время работы. Основная опасность, которую несут эти дефекты представляется в уменьшении толщины шва.
- При выполнении сварки встык, сварной шов не всегда полностью заполняет область разделки. Это приводит к образованию своего рода подреза, который уменьшает площадь стыковки труб. Неравномерное соединение концентрирует в себе все напряжения. В дальнейшем этот участок может привести к разрушению сварного шва и трубопровод разгерметизируется.
- Трубы соединяют, нанося несколько сварных швов. Иногда верхний слой может не полностью закрывать нижний или смещаться, образуя наплыв. Нарушение технологии приводит к уменьшению плотности прилегания верхнего шва.
- К внутреннему дефекту можно отнести случаи непровара. Это следствие неполного расплавления кромок металла. Образуется этот дефект при нарушении температурного режима сваривания. Такой участок соединения также является областью скопления напряжений. Результатом может стать образования разрыва на данном участке.
- Перечисленные выше поры и раковины могут быть в большем количестве и меньшего размера. Это приводит к тому, что металл сварного шва имеет пористую структуру.
- Если не зачистить поверхность или кромки перед началом работы, имеется риск попадания инородных предметов внутрь шва. Попросту говоря, шов может содержать в себе мусор. И вопросы в таком случае возникают к исполнителю работ.
- Выше мы говорили о нарушении температурного режима во время сварочных работ. Что приводит к непроварам. Однако, если температура превышает необходимую, можно просто прожечь деталь. Результатом прожога станет характерный наплыв с внутренней стороны.
Чтобы предотвратить негативные последствия перечисленными дефектами и уделяют достаточно большое внимание дефектовке. Все методы контроля и проверки качества выполняют без подвергания разрушению сварного соединения.
Методы, которые подразумевают разрушения, проводят исключительно в целях испытаний в лабораторных условиях.
Причиной использования на практике методов неразрушающего контроля очевидны, ведь он не подразумевает демонтаж участка сварки и/или доставки его в лабораторию. Исследуют сварные швы непосредственно на участке работы и используют различное оборудование для этого. Сегодняшние технологии позволяют применять весьма компактные приборы.
Выполнение неразрушающего контроля не означает пренебрежительное или неточное исследование. Этому процессу уделяют достаточно много внимания. Выполняют ее квалифицированные и специально обученные этому процессу специалисты.
Методы контроля без проведения разрушений

1. Визуально-измерительный
Методика проведения внешнего контроля путем осмотра и проведения измерений. Довольно простой метод, но не обладающий высокой точностью. Позволяет оценить наличие дефектов только снаружи.
Несмотря на то, что метод не дает исчерпывающих показаний, его используют в обязательном порядке. Это как метод хорошего тона. До того как перейти к следующему методу оценки, нужно обязательно провести визуально-измерительный контроль.
На самом деле, если дефект будет обнаружен на этой стадии, нет смысла проводить следующий вид определения контроля. Ведь для более детального изучения шва необходимо дорогостоящее оборудование.
В части измерений не используют что-то специфическое. Применяют инженерные измерительные приборы, достаточно точно позволяет произвести замеры используя штангенциркуль. До проведения измерений место очищают (в т.ч. от шлака) и обезжиривают.
Если говорить за визуальным метод определения, то могут использовать лупу. Она позволяет разглядеть довольно мелкие трещины. По итогам проведения данного контроля необходимо получить характер дефекта и его размеры.
2. Радиографический контроль
Метод дефектоскопии, который подразумевает использование приборов для проведения звуковых исследований внутри сварного шва. Звучит сложно, но на самом деле метод довольно прост. Он требует использование специального прибора, который анализирует пропускаемый через металл звук.
Полученный результат должен быть однородным. Если же внутри шва присутствует какая-то неоднородность или дефект, прибор отразит его основываясь на скорости движения звука.
Каноны проведения звукового исследования:
- использование ультразвука высокой частоты на участке сварного соединения;
- направление звуковой волны в область изучения структуры металла;
- улавливание отразившегося звука. Если он определяет препятствие, звук отражается быстрее.
3. Контроль с использованием магнита
Метод схож с предыдущим и подразумевает внутреннее изучение металла. В этом случае принцип воздействия на изучаемую зону металла базируется на магнитной проницаемости. В этом методе используют не звуковое влияние, а воздействие магнитными волнами.
Пуская магнитную волну в область шва прибор считывает скорость ее отражения. При наличии препятствия в металле, волна такое препятствие огибает. Прибор считывает скорость движения магнитной волны.
Применение данного метода дефектоскопии подразумевает использование специального прибора, способствующего создавать электромагнитные волны. Что следует обозначить из особенностей, то на поверхность подверженную исследованию наносят специальный порошок. Вместо порожка может использоваться жидкая суспензия.
Как часть этого метода, могут наносить на поверхность магнитную пленку, на которой проявляются все дефекты соединения. Такой метод получил немного другое название – магнитография.
Полученные на пленки данные считываются специальным дефектоскопом. Полученная информация отображается в виде изображения или же может быть представлена звуком.
4. Капиллярный метод дефектологии
Метод заключается на нанесении на металл специальной индикаторной жидкости, которая позволяет проникать в металл на капиллярном уровне. После этой жидкости остаются следы, которые позволяют определить поверхностные или сквозные дефекты. Данный метод позволяет выявить дефект и определить его размеры.
Такими жидкостями могут выступать керосин или бензол, скипидар и различное масло.
На сегодня существует различное капиллярное оборудование. Однако существует старый проверенный метод, который носит название проверки на «мел-керосин». Происходит это следующим образом:
- на поверхность сварного шва наносят мел (или допускается применение каолина);
- после высыхания, остатки мела убирают;
- далее наносят керосин и выжидают около полу часа;
- если на обратной стороне обнаружены подтеки, значит шов бракованный.
Для облегчения визуального контроля применяют специальные пигментные включения в индикаторные жидкости. Это может как обычный краситель яркого цвета, так и пигмент с люминесцентным свечением. Последний позволяет ускорить обнаружение дефекта с помощью ультрафиолетовой лампы.
Послесловие
Выше были рассмотрены основные методы дефектоскопии сварных швов. Некоторые из них просты, а некоторые требуют использование специального оборудования.
Что касается трубопроводов небольшого диаметра и на участках, которые не носят характер повышенного контроля, то могут применяться и другие методы контроля.
Суть заключается в проведения испытаний. Участок трубопровода подвергают испытанию гидравлическим методом или пневматическим. Рабочие среды подаются в систему под давлением.
При использовании жидкости бракованный шов начнет отпотевать. Если используется воздух под давлением, то на поверхность можно нанести мыльный раствор. При появлении пузырей, шов дефектный.
Перечисленные методы контроля производят без разрушения и позволяют идентифицировать бракованный шов непосредственно на месте участка работы.
Вероятность обнаружения неравномерности шва используя ультразвук или магнитное воздействия практически стопроцентная. Помимо общего обнаружения, исследования позволяют разобраться в причинах дефекта.